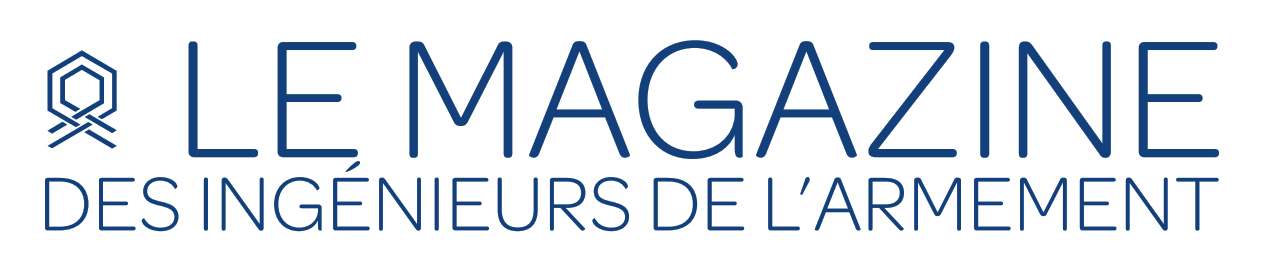
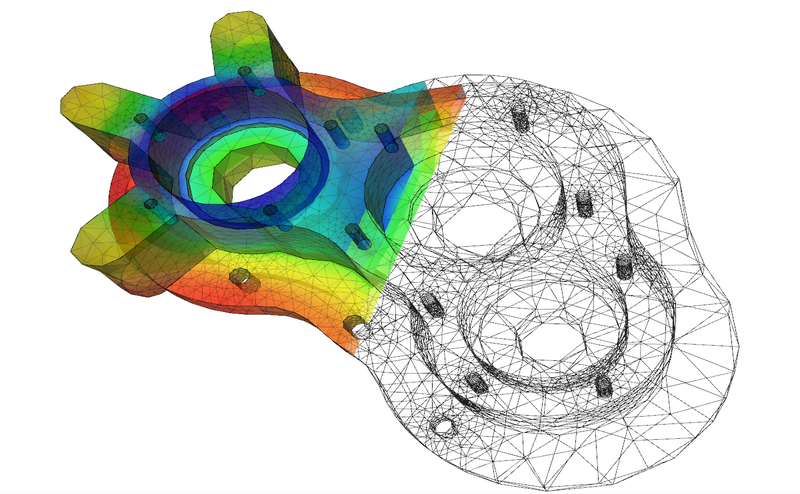
PERSPECTIVES EN MODÉLISATION NUMÉRIQUE
La modélisation numérique « physique » est au cœur de la conception de nos systèmes critiques, et présente un potentiel de progrès encore important, en vue de la réduction des cycles de conception. Ces progrès portent autant sur la modélisation de la physique elle-même que sur la mise en œuvre des modèles dans les chaînes de conception. En parallèle l’émergence des techniques d’apprentissage automatique (intelligence artificielle) offre une voie complémentaire qui pourrait se combiner à terme avec la modélisation physique classique pour tirer parti de l’expérience et modéliser le comportement individuel des systèmes en service
LA MODÉLISATION PHYSIQUE RESTE UNE DES CLEFS DE LA PERFORMANCE ET LA MAÎTRISE DE NOS SYSTÈMES HAUTEMENT CRITIQUES
C’est particulièrement vrai pour les produits de Safran, complexes et soumis à des environnement incroyablement sévères, au premier rang desquels les moteurs aéronautiques : les aubes de turbine, par exemple, évoluent aujourd’hui à des températures supérieures à 1600°C, plus de 500°C au dessus du point de fusion de l’alliage monocristallin qui la compose, et ce en utilisant de la manière la plus parcimonieuse possible l’air de refroidissement (à plus de 600°C quand même !) prélevé sur le compresseur, que l’on calibre au dixième de % près pour éviter de perdre en rendement du moteur. Le tout en subissant des efforts centrifuges colossaux et des cyclages thermiques violents (en particulier pour les moteurs d’avion de combat).
Ce n’est donc pas sans raison que très peu d’entreprises dans le monde ont la capacité de réaliser de tels objets qui doivent satisfaire un compromis subtil entre une somme incroyable de contraintes multi-physiques contradictoires (mécanique, thermique, aérodynamique, et même corrosion, …). Face à ces défis, les progrès de la modélisation physique (aérodynamique, combustion, mécanique des structures, comportement des matériaux, thermique et leurs combinaisons) mais aussi de sa mise en oeuvre (via la Conception Assistée par Ordinateur et la maquette numérique) ont été une des clefs ayant permis des gains spectaculaires de performance des moteurs depuis les premiers turboréacteurs (gains de facteur 4 à 5 en rapport poussée sur masse, ou en consommation spécifique pour les moteurs civils).
Par exemple, les techniques avancées de modélisation de la combustion (Large Eddy Simulation) développées par nos partenaires scientifiques, notamment le CERFACS, nous permettent aujourd’hui, sur des calculateurs hautement parallèles, de prévoir et d’éviter des phénomènes d’instabilité de combustion, souvent rédhibitoires, qui auparavant pouvaient être découverts au banc d’essai en cours de développement !
Ces techniques de modélisation dites “haute-fidélité” restent aujourd’hui largement à transposer à des problèmes hautement complexes, tels que la prévision du fonctionnement transitoire des compresseurs multi-étages, qui reste difficile avec les techniques de modélisation aérodynamique classiques (dites Reynolds Averaged Navier-Stokes), et est pourtant au cœur du fonctionnement du moteur.
Face à la complexité des phénomènes multi-physiques mis en œuvre, nous arrivons aux limites de l’approche de modélisation “monolithique”, c’est-à-dire un seul code de calcul appliquant une seule modélisation sur un objet complet, éventuellement bouclé avec un autre calcul mono-physique (soit en parallèle soit en séquentiel). Nous devons passer à une approche dite “multi-physique / multi-fidélité” où plusieurs modélisations, avec plusieurs niveaux de fidélité et plusieurs physiques, vont être imbriquées au sein d’un même objet : pour donner un exemple simple, on utilisera la haute-fidélité, très coûteuse et difficile à maîtriser, seulement dans les zones critiques pour l’instationnarité du compresseur, et des modélisations plus simples (et robustes) dans les autres zones…
VERS UNE MODÉLISATION MOSAÏQUE, SPIRALE, MULTI-MÉTIERS, POUR DES RÉDUCTIONS DE CYCLE DE CONCEPTION
Champ de température dans une chambre de combustion. Les techniques avancées de modélisation de la combustion sont utilisées couramment en conception des chambres de combustion et permettent de prévenir des problèmes autrefois découverts au moment des essais.
On passe ainsi du “Monolithe” à la “Mosaïque”, d’où le nom de “MOSAIC” donné à la nouvelle plateforme de modélisation orientée mécanique des fluides développée par Safran avec ses partenaires scientifiques, et notamment l’ONERA.
Dans MOSAIC, ce n’est plus le code de calcul qui est au centre du jeu, mais les données décrivant le problème et la stratégie de modélisation (“le workflow de modélisation”), qui peut inclure différentes étapes de « dégrossissage » avec des modélisations simplifiées, suivies de phases d’optimisation de géométrie, avant des calculs fins enchaînés sur différents points de fonctionnement. MOSAIC constitue une sorte d’OS (Operating System) qui va faire fonctionner selon la bonne séquence les différentes briques de modélisation, leur faire échanger des données, et collecter le résultat final ainsi que tous les résultats intermédiaires, tout en optimisant l’usage des ressources de calcul.
MOSAIC illustre une tendance importante en termes de modélisation : pour gagner en efficacité et réduire les cycles de développement, la mise en œuvre de la chaîne de conception devient aussi importante que la qualité de la modélisation physique sous-jacente.
L’objectif est d’être capable d’enchaîner sans couture des phases d’ingénierie système du produit, et la montée en maturité de sa conception et de son industrialisation, en faisant travailler réellement en parallèle les différents métiers sur la base de modèles 3D communs et de modélisations montant en niveau de fidélité au cours des phases de conception. Les progrès de la CAO (paramétrable, partageable, rejouable) et les approches de “Workflow” illustrées par Mosaic sont au coeur de cette approche en “spirale”.
Nous avons ainsi pu montrer sur le cas des aubes de turbine, que nous pouvions diviser par 5 à 7 le temps d’une itération complète de conception incluant la fabricabilité (simulation de fonderie), et donc de faire beaucoup plus d’optimisations dans un temps donné pour un meilleur résultat. L’objectif, ambitieux, doit être maintenant de généraliser ces méthodes dans le groupe Safran.
On le voit, Safran est depuis de nombreuses années à la pointe de la modélisation “classique” reposant sur la résolution approchée des équations de la physique. Nous disposons d’équipes nombreuses et d’un réseau scientifique reconnu, et cela restera pour longtemps un axe important d’investissement.
En parallèle, une autre approche est en plein essor depuis quelques années : l’apprentissage automatique (“Machine Learning”), qui consiste à construire des modèles empiriques (dits souvent “boîte noire” car ne contenant pas d’explication physique) à partir d’une base d’expérience, c’est-à-dire de données. L’apprentissage consiste en l’optimisation statistique des très nombreux paramètres d’un modèle mathématique ou algorithme (par exemple un réseau de neurone) pour que ce dernier fournisse les réponses attendues sur le jeu de données présenté.
L’essor récent, fulgurant, de techniques souvent anciennes dans leur concept résulte de la combinaison de trois facteurs : d’abord l’accès à une capacité de calcul permettant d’apprendre et de rejouer des modèles comportant un nombre colossal de paramètres (par exemple les réseaux de neurones dits profonds), puis la disponibilité de grandes masses de données liée à la numérisation (exemple : photographie numérique), et enfin la performance remarquable de ces approches sur certains problèmes tels que la reconnaissance d’objets dans des images, pour laquelle les approches de type “Deep Learning” ont totalement supplanté en quelques années seulement les approches classiques de traitement d’image.
LE “MACHINE LEARNING” : UNE APPROCHE EN PLEIN ESSOR
Safran s’est bien évidemment emparé de ces progrès techniques pour en explorer le potentiel, notamment au sein de Safran Tech, notre centre de R&T, et Safran Analytics notre centre de compétences sur les données.
Un premier domaine d’application ciblé a été le traitement d’image, pour les chaînes optroniques mais aussi pour les contrôles non destructifs en production. Cette dernière application peut sembler anecdotique, mais il faut comprendre qu’il n’en est rien : sur nos pièces les plus critiques, notamment celles des moteurs, le temps de contrôle peut représenter plus de 30% du temps total de fabrication. La numérisation de techniques telles que la radiographie, l’introduction de la tomographie numérique, et la substitution de techniques ancestrales de contrôles (ressuage, magnétoscopie) par des techniques “numériques”, permettent de passer à l’étape suivante : l’automatisation de la sanction des défauts.
La mise en œuvre de techniques de machine-learning dont le deep-learning permet par exemple la sanction automatique, en production série, d’une partie des défauts des aubes de soufflante en composite tissées 3D du moteur LEAP, et l’aide à la sanction pour les défauts les plus complexes. Avec à la clef des gains de temps considérables et une réduction de la pénibilité du travail pour les opérateurs. Les mêmes techniques sont appliquées aux aubes creuses de turbine.
Un deuxième domaine d’application est la perception de l’environnement, notamment dans le domaine du véhicule autonome, terrestre et aérien. Dans notre laboratoire commun avec PSA et Valeo, situé dans notre centre Safran Tech à Saclay, nous mettons en œuvre des algorithmes d’intelligence artificielle permettant d’identifier des véhicules, des piétons, et de prendre des décisions telles que, par exemple, s’insérer dans un rondpoint pour un véhicule terrestre. Ces techniques sont appliquées dans notre véhicule terrestre autonome de démonstration E-RIDER, destiné aux applications défense, et au cœur du PST Furious, dans lequel nous étudions, sous contrat de la DGA, la mise en œuvre collaborative de différents types de véhicules terrestres autonomes et de drones dans un cadre de combat terrestre. Dans ce domaine, nous combinons la modélisation physique (simulation de la scène et des capteurs, jusqu’à la constellation GPS) et l’intelligence artificielle pour la perception et la décision.
Un troisième domaine est celui de la maintenance prédictive de nos équipements en service, pour améliorer leur disponibilité et réduire le coût en service. La vision sous-jacente est de pouvoir individualiser le comportement de chaque exemplaire du produit, au travers des données recueillies pendant son cycle de vie et d’une modélisation de son comportement, pour constituer un “jumeau numérique” ? Celui-ci représentera l’état de configuration et de vieillissement du jumeau physique, sur la base duquel des décisions de maintenance “sur mesure” pourront être prises, par opposition aux décisions fondées aujourd’hui sur des usages, comportements, et marges de sécurité moyennés.
Ces approches seront appliquées au travers de « plateformes » permettant de recueillir et partager les données. Safran a ainsi lancé, par exemple, la mise en place d’une plateforme sécurisée destinée à héberger les données de ses clients et à leur fournir des applications telles que BOOST® (Bank of Online Services & Technologies) qui permet aux clients de Safran Helicopter Engines d’avoir accès en tempsréel, aux données personnalisées de leurs moteurs afin d’optimiser la maintenance de leur flotte.
VERS UNE COMPLÉMENTARITÉ ENTRE MODÉLISATION PHYSIQUE ET IA POUR LA CONCEPTION
Le dernier domaine d’emploi prioritaire est la conception des produits et systèmes, dans lequel l’intelligence artificielle pourra être utilisée pour concevoir des produits plus rapidement à partir des données d’expérience. La fin de la prééminence de la modélisation physique ?
Non : les succès remarquables rencontrés par l’intelligence artificielle dans la résolution pratique de certains types de problème pourrait laisser penser qu’à terme il n’y aura plus besoin de modélisation physique et qu’il suffira de faire apprendre des modèles sur des données d’expérience pour construire des prévisions ou des extrapolations fiables à de nouvelles conceptions. Cette vision est simpliste : en réalité l’apprentissage automatique a ses avantages et ses limitations et il sera plutôt complémentaire des modélisations classiques que concurrent dans de nombreux cas.
A titre d’exemple, une de ses limitations majeures est la difficulté à « démontrer » un niveau de confiance dans le résultat fourni, car l’algorithme est le plus souvent non « explicable » (en particulier pour les réseaux de neurones profonds) ce qui pose de véritables défis pour les systèmes critiques et la certification. Un des avantages est a contrario de pouvoir, à partir des données, extrapoler des solutions qui ne seraient pas nécessairement formulées par un raisonnement humain, et ce, très rapidement. Ainsi un scénario d’emploi simple en conception consisterait en l’utilisation d’un algorithme d’IA pour proposer des conceptions candidates à une spécification donnée, à partir des données d’expérience historiques disponibles sur des objets similaires. Ensuite, ces conceptions seraient modélisées physiquement pour les comparer et démontrer leur performance.
Comme évoqué précedemment, les systèmes critiques doivent satisfaire un nombre important de contraintes multi-physiques (auxquelles peuvent s’ajouter des considérations sur le processus de fabrication ou le coût de maintenance). L’IA pourrait également être d’une aide précieuse pour aider à explorer rapidement et synthétiser les résultats - des millions de points - des calculs physiques associés.
L’IA sera ainsi une des briques importantes du « Workflow » de conception que j’ai décrit plus haut. Mais nous n’en sommes encore qu’au début de l’histoire !
Aucun commentaire
Vous devez être connecté pour laisser un commentaire. Connectez-vous.