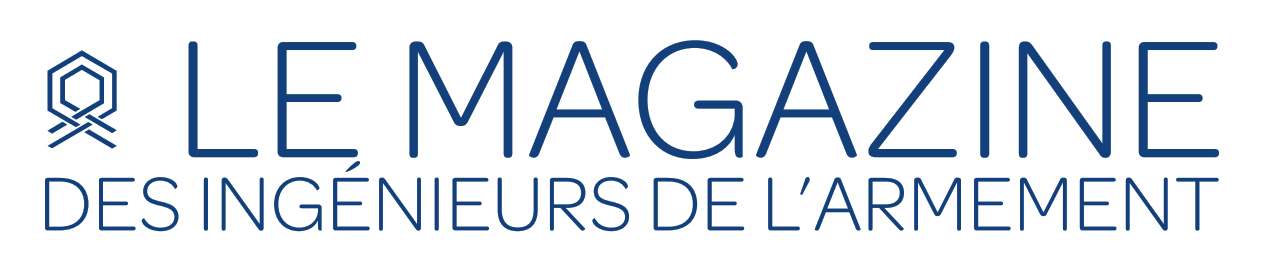

D’UNE INDUSTRIE TRADITIONNELLE À L’USINE 4.0
LA PRODUCTION DE MUNITIONS EN MOYENNE ET GRANDE SÉRIE
Des robots pour capter des parts de marché, d’accord... mais pour créer des emplois ? Retour d’expérience chez Nexter Munitions.
Consommables par nature, les munitions n’en sont pas moins déterminantes sur le champ de bataille. Elles doivent être aussi sûres et simples d’emploi qu’efficaces dans les effets recherchés. Leur cahier des charges s’enrichit à l’aune des opérations extérieures : versatilité des effets, insensibilité aux agressions, portée accrue, maîtrise des dommages collatéraux, programmation avant le tir ou en vol. Le système complexe ainsi défini doit, selon les calibres, supporter des accélérations positives et négatives jusqu’à 100 000 g, subir une perturbation jusqu’à Mach 5 en sortie de canon, parcourir jusqu’à 40 km et atteindre sa cible avec précision.
Cette performance est un inducteur de coût, mais les clients s’étalonnent par rapport au marché mondial, où l’intensité concurrentielle croît : la dérive des prix n’est donc pas une option. Pour rester compétitif, il faut augmenter les volumes en captant des marchés export – 80% du carnet – et adapter l’outil industriel en permanence.
La production annuelle atteint quelques milliers de composants pour les missiles et l’espace, quelques dizaines de milliers d’obus de char et d’artillerie, et plusieurs centaines de milliers de cartouches de moyen calibre (du 20 mm au 40 mm). Les révolutions industrielles actuelles répondent bien aux enjeux, à commencer par la robotisation.
Des investissements soutenusDe 2013 à 2017, Nexter a investi 33 M€ dans l’outil industriel, dont 13 M€ directement liés à l’automatisation. Les sites de Tarbes et de La Chapelle comptent à ce jour 31 chaînes automatisées dont 22 robots. Le taux de robotisation s’établit ainsi à 385 robots pour 10 000 employés. |
A titre d’exemple, la préparation des corps d’obus de gros calibre comprend des opérations d’usinage et de ceinturage à partir d’une ébauche forgée, une épreuve en pression et de multiples contrôles. Réalisée sur un îlot robotisé, cette séquence ne nécessite qu’un opérateur au lieu de quatre avec une chaîne traditionnelle. De ce fait, cette étape critique pour la performance et la sécurité du produit, auparavant sous-traitée dans un pays à moindre coût de main d’œuvre, a pu être réinternalisée. La maîtrise des paramètres process et des caractéristiques mécaniques est améliorée.
Un cobot pour un poste d’assemblage mécanique.
D’autres unités automatisées ont engendré des gains comparables : traitement de surface et contrôle des douilles de moyen calibre, fixation des amorces, chargement des traceurs, encartouchage, contrôle radio des fusées...
A-t-on pour autant des usines sans personnel ? Bien au contraire : en cinq ans, le chiffre d’affaires s’est apprécié de 75 % et l’effectif de 10 %. Cependant les métiers évoluent rapidement : l’automaticien spécialiste est devenu incontournable ; la qualification des opérateurs s’accroît, jusqu’à bac +2 sur certaines lignes ; la formation interne et le référentiel de recrutement doivent s’adapter.
A contrario, il eût été impossible de pérenniser l’activité sans recourir à l’automatisation, face à des concurrents bénéficiant de faibles coûts de main d’œuvre ou de grands marchés intérieurs. Ainsi, le rapport 10 entre les budgets de défense des Etats-Unis et de la France se retrouve dans les commandes annuelles d’obus d’artillerie.
Les apports multiples des nouveaux procédés
Outre la compétitivité et la qualité, les robots améliorent grandement la sécurité et l’ergonomie. La réduction des interventions humaines en zone pyrotechnique est un progrès évident, ainsi que l’assistance des robots dans la manipulation d’obus pouvant peser jusqu’à 43 kg pour l’artillerie de 155 mm. En partenariat avec CEA Tech, Nexter expérimente des « cobots » afin de sécuriser des postes de travail où l’homme est irremplaçable par la finesse de son geste.
Enfin, l’automatisation des chaînes permet de disposer d’une masse d’informations de process qu’il reste à exploiter : réglages, mesures dimensionnelles, acquisitions vidéo par exemple. Un projet pilote concerne la chaîne d’encartouchage des obus de 40 mm télescopés. Destinés notamment au JAGUAR de l’armée de Terre dans le cadre du programme SCORPION, ces obus compacts et performants bénéficient d’une traçabilité intégrale. Tout au long de la chaîne robotisée, qui fonctionne sans intervention humaine, les paramètres utiles sont enregistrés sur une puce RFID. Un QR code marqué sur l’obus lui associe son historique de fabrication. L’apport déterminant de qualité bénéficiera in fine aux clients, dès les premiers lots série de cette année. Ensuite, l’exploitation de ces données améliorera la maîtrise des paramètres critiques de process et de conception.
Ces techniques ne sont pas réservées aux ateliers à grande capacité. Le site de Tarbes de Nexter, spécialisé dans les initiateurs, fabriquera les détonateurs opto-pyrotechniques dont chaque ARIANE 6 embarquera quelques dizaines d’exemplaires. Cette technologie de rupture fait appel à l’énergie laser transportée par fibre optique pour initier une chaîne pyrotechnique produisant une onde de choc calibrée. L’atelier de production est entièrement numérisé, contribuant à la maîtrise du coût unitaire d’assurance qualité, malgré des exigences élevées rapportées à de petits volumes.
Aujourd’hui limitée à des fonctions d’aide au diagnostic, comme l’analyse d’assemblages mécaniques complexes par tomographie 3D, l’intelligence artificielle devrait rapidement étendre son champ d’application dans ces nouveaux ateliers. Elle est également explorée par la direction technique pour capitaliser de l’expertise par « deep learning ».
Un obus guidé (ici à l’ONERA) comprend de nombreuses pièces en fabrication additive
Pour conclure ce rapide tour d’horizon, la fabrication additive d’alliages à très haute résistance s’est imposée dans plusieurs produits novateurs, têtes militaires à effets modulables ou prototypes d’obus de précision. Dans ce dernier cas, la masse et le temps de montage du module de guidage, ou « Canard Actuation System », ont été divisés par deux. Le défi est multiple : il s’agit d’apprendre à spécifier, concevoir, qualifier et contrôler cette technologie déroutante. La tenue au coup de canon est excellente – pas loin de 20 000 g – ce qui est de bon augure pour une production série espérée prochaine !
Aucun commentaire
Vous devez être connecté pour laisser un commentaire. Connectez-vous.