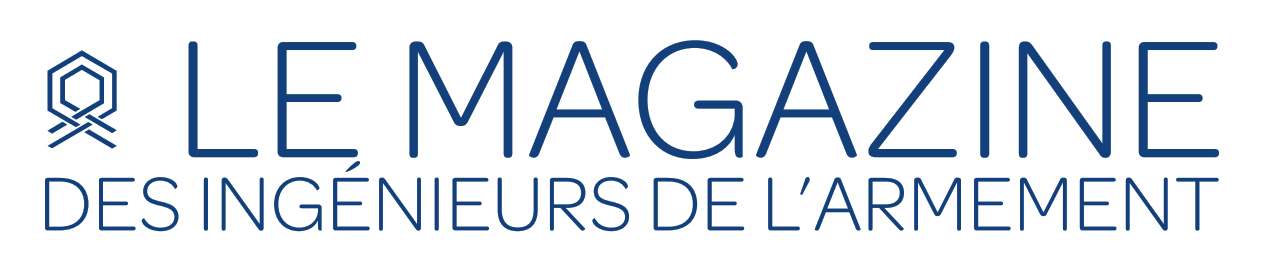
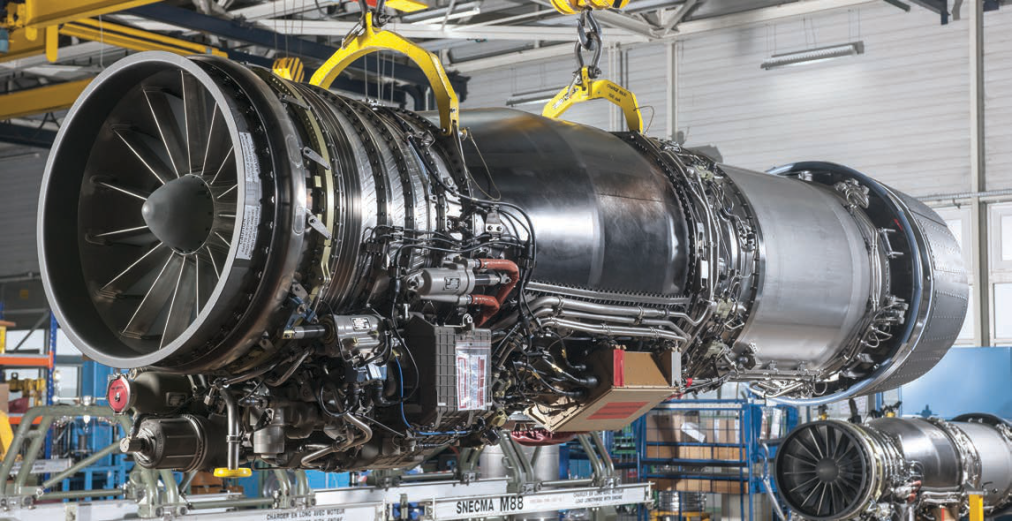
LE MOTEUR DU RAFALE, LA PERFORMANCE MAÎTRISÉE
On attend d'un moteur d'avion de combat avant tout de la performance, mais le moteur M88 du Rafale, concentré de technologies, innove aussi sur la maintenabilité et a fait l'objet d'une amélioration continue de son coût de possession. C'est le fruit d'une collaboration exemplaire entre l'industrie, la DGA et les forces armées.
Un de mes grands souvenirs d'ingénieur de l'armement est d'avoir, lorsque j'avais trente ans et que j'étais architecte M88 à la DGA, arpenté le pont du Charles de Gaulle et senti, littéralement dans ma chair, la vibration lancinante des deux moteurs du Rafale. Une sensation de puissance tout aussi marquante que lorsque le pilote déchaîne, en présentation en vol, les 15 tonnes de poussée rugissante des deux moteurs en post-combustion !
Puissance, compacité, rapport poussée sur masse, c'était avant tout le défi de la motorisation pour Snecma et la DGA au lancement du programme. Il s'agissait de répondre aux besoins d'un avion ambitieux, poussant la polyvalence à un niveau jamais imaginé (et jamais égalé) et de développer un moteur au meilleur niveau mondial.
Un concentré de technologies
Par rapport au moteur M53 du Mirage 2000, le saut technologique était majeur : un moteur double corps, une régulation complètement numérique, des aubes de turbine en alliage monocristallin, des disques aubagés monoblocs dans le compresseur, des nouveaux alliages en métallurgie des poudres, un canal flux froid en composite « tiède », des volets extérieurs de tuyère en composite à matrice céramique (la première application au monde en aéronautique), un nouveau concept de réchauffe... Ces technologies avaient fait l'objet d'études amont depuis la fin des années 1970 pour certaines, mais le passage à l'application industrielle n'en représentait pas moins un saut considérable.
Un des sauts technologiques les plus importants a concerné les aubes de turbine. Il s'agit des ailettes du rotor de l'étage de turbine situé directement derrière la chambre de combustion. Pour faire simple, il s'agit d'une « éolienne » qui entraîne le compresseur - situé en amont du moteur - grâce à l'énergie de l'air comprimé et réchauffé qui se détend en mettant en mouvement la turbine. L'augmentation de la température d'entrée dans la turbine est un - sinon le - paramètre primordial ayant permis aux moteurs d'avion de combat de gagner en compacité et en rapport poussée sur masse de manière spectaculaire. A titre d'exemple, le M88 est plus petit que le seul canal de post-combustion du moteur ATAR 9K50 du Mirage F1 alors qu'il a une poussée supérieure ! La température d'entrée turbine sur le Rafale est de près de 1 600 °C, 1 200 °C sur le Mirage 2000 et seulement 900 °C sur Mirage F1.
Cependant, cette augmentation pose un défi majeur pour la tenue des aubes de turbine. Ces aubes sont soumises à des efforts centrifuges énormes : chaque ailette de 10 cm de haut est soumise à une force centrifuge de l'ordre de 15 tonnes qui tend à l'étirer et l'arracher, et ce dans un air à 1 600 °C. Il faut donc des matériaux extraordinaires : des superalliages monocristallins à base nickel. Dans ces matériaux, pour améliorer la résistance en fluage, on supprime tous les joints de grain : pour ce faire la pièce entière doit être constituée d'un seul cristal d'alliage - un peu comme un diamant. On peut obtenir cela grâce à un procédé sophistiqué de fonderie.
Mais où cela se complique encore, c'est que ces alliages ont une température acceptable de fonctionnement limitée, de l'ordre de 1 100 °C. Il faut donc que les pièces soient refroidies - par de l'air à 600 °C, considéré comme tiède par un motoriste ! Elles sont donc creuses avec des canaux complexes de refroidissement, des micro-perçages permettant de générer des films d'air frais en surface. Et comme cela ne suffit encore pas, elles sont recouvertes d'une « barrière thermique » - couche de céramique isolante micro-texturée obtenue par un procédé complexe ! Seuls les motoristes majeurs maîtrisent ces technologies et leur bonne combinaison grâce auxquelles le Rafale peut jouer dans la cour des grands.
Un souci permanent de maintenabilité et de coût de possession
Sur un avion, le moteur est le principal poste de maintenance, aussi l'innovation a-t-elle porté dès le départ sur le concept de maintenance : grande accessibilité du moteur et des équipements dans l'avion, modularité, mais aussi un concept très innovant « zéro aire de point fixe » qui permet de remettre en service un moteur après maintenance sans aucun essai de mise à feu, sur banc ou sur avion au sol... Des éléments essentiels pour le client et qui constituent un des atouts du Rafale au-delà de sa performance opérationnelle. Pour la première fois, l'Armée de l'air opère un moteur sans le moindre banc d'essai, ni dans les forces ni au SIAé. Une économie substantielle et une grande flexibilité opérationnelle en termes de projection.
Au-delà de ces choix structurants sur le concept de maintenance, l'effort a été porté dès le départ sur l'amélioration permanente de la durée de vie des parties chaudes et sur l'augmentation des intervalles d'inspection des pièces critiques à limite de vie (les disques de turbine et de compresseur), pour améliorer la disponibilité et réduire le coût de maintenance, un enjeu essentiel pour le client.
Ainsi, sur près de quinze ans, la DGA et Snecma ont conduit ensemble une série de démonstrateurs : TOP, PHT, TOP+, THEO, ECO, permettant de tester et démontrer des améliorations technologiques des aubes de turbine, qui ont permis une succession d'évolutions incrémentales du moteur, se caractérisant à chaque fois par une amélioration de plusieurs centaines d'heures de la durée de vie des aubes, jusqu'à la dernière version M884E (dite pack CGP pour coût global de possession) qui permet d'atteindre une durée de vie de 4 000 TACs (tactical air cycles) contre 2 500 TACs pour la version précédente.
J'ai eu la chance de participer en tant que client et puis industriel à des étapes importantes de cette aventure et je suis personnellement fier de ce que nous avons accompli, et qui contribue à faire du Rafale un succès opérationnel.
Aucun commentaire
Vous devez être connecté pour laisser un commentaire. Connectez-vous.