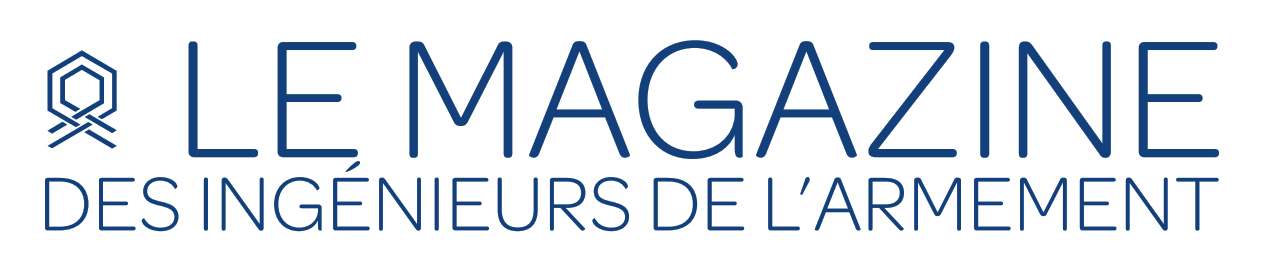
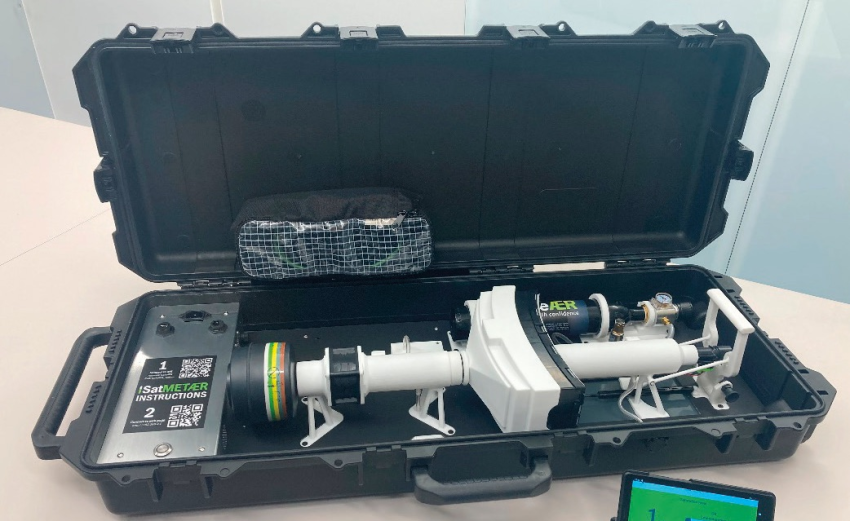
SAFEAER UNE STARTUP POUR UN PROBLEME VIEUX DE 100 ANS
L’histoire commence au beau milieu de l’été 2018. Alors que je m’apprête à quitter la tête du département protection de DGA Maîtrise NRBC pour partir en affectation temporaire dans l’industrie, je rassemble une petite équipe pour tester une idée que je mature depuis plusieurs années, et qui pourrait bien révolutionner le monde de la filtration chimique…
« Qui ose gagne » Colonel Jean Sassi
Pour que le lecteur comprenne de quoi il retourne, petit flash-back 100 ans plus tôt ; la première guerre mondiale a vu apparaître les armes chimiques. L’élément clé de la protection respiratoire est la cartouche filtrante, composé de charbon actif, qui arrête les gaz toxiques tout en ayant le bon goût de laisser passer l’oxygène et l’azote. Améliorée tout au long du XXe siècle, cette technologie est toujours utilisée dans le domaine militaire (masques à gaz, filtrage de l’air dans les espaces confinés comme les chars, sous-marins, etc.), mais également largement déployée dans le secteur civil pour l’épuration de l’air (engins agricoles filtrés, secteur nucléaire, retraitement d’effluents gazeux …). Cela représente ainsi un marché annuel de la classe 10 milliards de dollars.
Les attaques au gaz Moutarde, cauchemar des poilus
Comme un filtre obéit aux lois de la physico-chimie, il se sature peu à peu en polluants, y compris en polluants que le filtre n’a pas vocation à arrêter. De ce fait, il est difficile d’estimer à quel moment le filtre doit être changé. L’ingénieur de l’armement, habitué à la gestion de risques, aux analyses de vulnérabilités et autres risques juridiques pour l’Etat se dit alors naturellement : mais comment puis-je mesurer l’efficacité de mon filtre ?
Aussi étonnant que cela puisse paraître, il n’existait pas en 2018 de mesure non destructive pour contrôler la saturation d’un filtre. On imagine bien les conséquences inconfortables en termes de contrôle de production, durée d’utilisation d’un filtre, réemploi éventuel, durée de vie en stockage. En bref : un risque pour la santé des utilisateurs, et des coûts superflus. On dit d’ailleurs encore dans les usines à des opérateurs de changer leurs cartouches filtrantes s’ils sentent une odeur inhabituelle… En voilà l’illustration parfaite !
C’est dans ce contexte que nous décidons donc de tester une approche radicalement différente. En n’utilisant que ce que nous avons sous la main, sans impacter le plan de charge, nous réussissons rapidement à mettre en évidence une piste très prometteuse.
« In a world that is changing really quickly, the only strategy that is guaranteed to fail is not taking risks. » M. Zuckerberg
L’acte II se joue un an plus tard. Je suis donc en affectation temporaire chez Safran Electronics & Defense, quand je découvre le programme « We love intrapreneurs », mis en place depuis peu par le groupe Safran. S’inspirant du modèle de l’entreprenariat, l’idée est de monter des start-ups internes, formées par des collaborateurs du groupe.
La valorisation des brevets étatiques restant une science peu développée – je l’ai expérimenté sur un premier brevet déposé auparavant – j’y vois l’opportunité assez unique de donner une suite industrielle au projet. Je dépose donc un dossier, et me retrouve quelques semaines plus tard devant un jury composé d’une partie du COMEX du groupe pour « pitcher » l’idée. C’est là que l’aventure se corse : étant dans le groupe seulement depuis 11 mois, j’ai trois semaines pour former une équipe polyvalente, solide, et motivée, qui soit prête à se lancer dans l’aventure à temps plein si nous sommes sélectionnés. Finalement, l’équipage se forme avec trois autres personnes issues de Safran Electronics & Defense et Safran Filtration Systems. Nous sommes sélectionnés en novembre 2019 comme huit autres équipes pour approfondir l’idée, en parallèle de notre poste, avec des formations et coaching de l’EM Lyon.
Nous croyons à notre projet, même pendant la période mars-août 2020 de crise Covid où je reviens au service de l’Etat – les experts en protection respiratoire vis-à-vis du risque biologique ne courent pas les administrations. – Et finalement, en septembre 2020, nous remportons la finale de la saison II de l’intraprenariat Safran, synonyme d’une forme de levée de fonds et un passage à temps plein sur le projet pour nous quatre.
« Innover, c’est facile. La difficulté, c’est de transformer une innovation en vrai business » Mikael Dell
Et depuis ? Après octroi d’une licence à Safran par l’Etat, nous avons développé notre premier produit que nous avons déjà mis entre les mains de clients, notamment dans le domaine de la Santé-Sécurité-Environnement. Avec une approche loin du build-to-spec classique du monde défense, notre logique de développement est foncièrement agile, avec pas moins de 10 itérations de notre prototype pour aboutir aux premiers de séries, produits en France au sein d’une usine du groupe. Le format d’équipe, réduit (nous quatre) et intégré, permet des prises de décisions en moins de 24h. Cela détonne un peu dans le fonctionnement habituel d’une grande organisation, mais quand on nous demande si notre photo de premier de série est une vue CAO ou une « vraie photo », on se dit qu’on ne fait pas totalement fausse route. Nous ne sommes bien entendus pas livrés à nous-mêmes, mais interagissons régulièrement en boucle courte avec nos sponsors issus du COMEX qui nous apportent leurs conseils d’une acuité toujours remarquable, tout en validant tous les 4 mois nos avancées via un « STOP OR GO ».
Loin des modèles d’ultra-spécialisation habituels, je suis amené, dans une même journée, à me pencher sur des problématiques d’approvisionnements de composants électroniques (il y a une pénurie en ce moment avez-vous dit ?), de tolérance mécanique, de physico-chimie, de business plan, de propriété intellectuelle, de relation clients ou fournisseurs, de cash-flow, de stratégie marketing… Et c’est peut-être le sens de ce projet qui nous pousse à toujours avancer, puisque quand on trouve des cartouches 100% saturées qui ont été utilisées par des ouvriers pour des procédés spéciaux, on sent que notre action devrait faire progresser la protection de la santé, et donc le bien commun.
Le 26 janvier, Benoît Chandesris recevait le prix Pierre Faure 2021Pierre Faurre, qui fut président de SAGEM serait heureux de voir que pour la première fois, un membre de son entreprise est récompensé du prix qui porte son nom ! Benoît Chandesris, en affectation temporaire chez Safran a su convaincre le jury de ses qualités de maîtrise technique, d’aptitude au management et de réussite dans le projet Safeaer qu’il porte depuis plusieurs années. Ainsi qu’il l’a exposé devant l’amphi .K le 26 janvier dernier, les ingrédients de Safeaer sont de partager une vision et une utilité, un travail en équipe, et surtout une posture d’innovation pour garder en tête l’objectif, quitte à adapter les moyens. L’anecdote du légionnaire furieux à la Courtine voyant qu’on avait rusé pour rentrer au camp sans traverser le cours d’eau a été bien comprise par tous les futurs polytechniciens innovateurs. Bel exemple et belle récompense pour cet arrière petit fils d’Henry Le Chatelier, physicien, inventeur et ingénieur conseil qui appelait les « ingénieurs français à être beaucoup plus présents dans les ateliers ». Eric labaye, président de l’X et Frédéric Oudéa, Président de la FX entourent le lauréat |
Aucun commentaire
Vous devez être connecté pour laisser un commentaire. Connectez-vous.