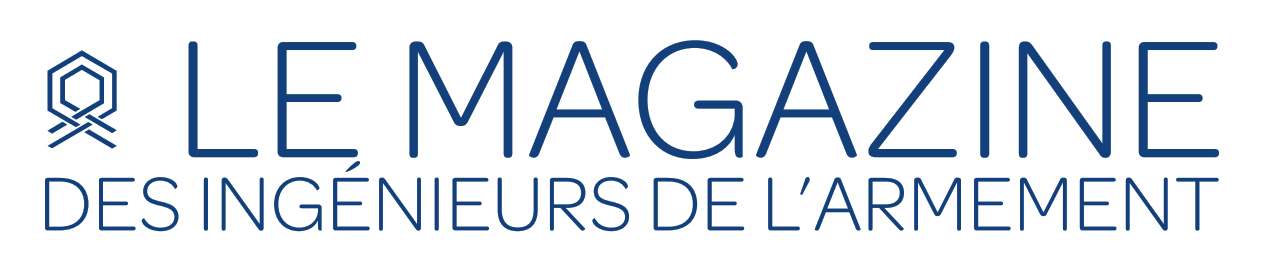
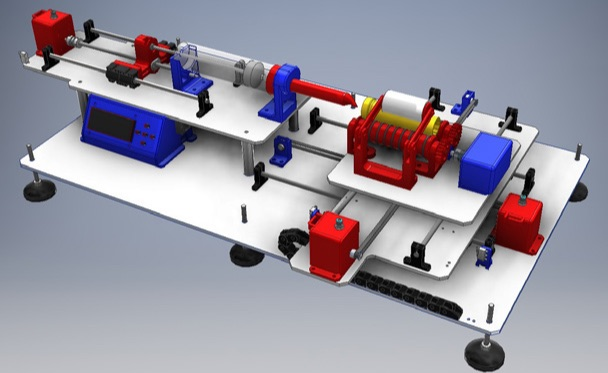
IMPRIMER DES EXPLOSIFS
UN ACCÉLÉRATEUR D’INNOVATION
Si l’utilisation industrielle de fabrication additive s’est fortement développée au cours de la dernière décennie, l’impression 3D de matériaux énergétiques n’est pour sa part maitrisée que par un tout petit nombre de sociétés dont EURENCO fait partie. Accélération des développements, amélioration des performances et nouvelles utilisations, de nouveaux horizons s’ouvrent pour la pyrotechnie
La fabrication additive appliquée aux matériaux énergétiques est une technologie de rupture que peu de sociétés maîtrisent. Si cette technologie permet de produire des chargements propulsifs ou explosifs à performances accrues dont l’architecture (forme ou empilement de matériaux) n’est pas réalisable par les procédés classiques, elle est également un accélérateur des phases de développement ou de mise en place d’améliorations. En gagnant en agilité et flexibilité, il est ainsi possible de développer et produire différents prototypes à partir d’un même outil sans avoir recours à de long processus de spécification et d’acquisition d’outillages spécifiques.
Ces nouveaux modes de fonctionnement doivent néanmoins concilier la capacité dite de « test and learn », que l’on appelle aussi le droit à l’échec, et la sécurité pyrotechnique qui ne permet pas l’erreur. Ils nécessitent de s’appuyer sur des compétences liées aux matériaux énergétiques, à la chimie et physico-chimie, aux propriétés mécaniques, aux phénomènes d’interfaces et d’adhésion entre couches sans oublier la modélisation/simulation. Si ce socle de compétences constitue une barrière d’accès pour de nouveaux entrants, les pratiques des sociétés historiques peuvent aussi constituer un carcan dont il peut être difficile de sortir.
Clara DEBIESSE – Ingénieure d’études en charge du projet au sein de l’IFTH puis au sein de EURENCO pour le transfert. « Compte tenu de la complexité du projet, détacher une ingénieure d’études sur le développement de cette innovation a permis de monter rapidement en compétence et d’acquérir un haut niveau d’expertise. Le partage des connaissances entre les deux parties (IFTH et EURENCO) tout au long de l’étude a été un élément clé pour atteindre les résultats souhaités depuis le prototype jusqu’à la production industrielle. »
|
Afin d’essayer de répondre à ces injonctions contradictoires, EURENCO a ainsi noué plusieurs partenariats afin d’accélérer la montée en maturité de l’impression 3D de matériaux énergétiques. Le principe est clair : s’ouvrir aux meilleures pratiques tout en assurant la sécurité pyrotechnique. Un partenariat a notamment été mis en place entre Eurenco et l’Institut Français du textile et de l’Habillement (IFTH).
Demi-coque incrément de mortier 60 mm
Grain de poudre
Tube allumeur
Des premiers prototypes ont été développés afin de mettre en évidence la qualité de définition des objets obtenus au sein de l’IFTH sur des matériaux inertes avant d’implanter, en 2021, un Fab Lab dédié à la fabrication additive de matériaux actifs sur le site d’EURENCO Bergerac.
Du laboratoire à la production de série :
Parallèlement à ces développements novateurs sur l’impression 3D de matériaux énergétiques, Eurenco a mis en application le principe de l’impression 3D pour le développement et la mise en production du Relai Initiateur Chargé (RIC). Ce tube initiateur des charges modulaires pour artillerie de 155 mm, dont EURENCO est l’un des leaders européens, constitue un élément crucial pour le fonctionnement et la performance de ce système.
Une démarche agile et itérative a été mise en place. Elle a fait appel à des compétences d’experts matériaux et produits, dont l’objectif était de fixer un cadre, associés à de jeunes ingénieurs et techniciens « sortant du cadre » du fonctionnement habituel. Une alchimie certaine s’est produite.
Les possibilités de l’impression 3D ont d’abord été utilisées aussi bien pour concevoir et réaliser les prototypes de l’imprimante 3D elle-même. Ce prototype a été conçu à partir d’imprimante 3D plastique mais aussi par la récupération de mécanismes d’anciennes imprimantes 3D. Des tests de répétabilité ont été réalisés afin de préindustialiser la solution et améliorer le dispositif. Cette démarche incrémentale rendue possible par les multiples possibilités de l’impression 3D ont permis de développer deux fois plus vite et pour trois fois moins cher un produit aux performances accrues. Cet objet fait désormais partie intégrante de la nouvelle charge modulaire MACS 100% conçue et maintenant produite entièrement par EURENCO et en service sur plusieurs systèmes.
Suite à cette phase agile et dynamique, de prototypage, d’industrialisation puis qualification, un atelier industriel a pu être mis en service à Bergerac moins de deux ans après la décision de lancement du programme.
Julien LOYER – Technicien chargé d’industrialisation « L’utilisation de l’impression 3D et de toutes ses possibilités s’est parfaitement intégrée aux nouvelles méthodes de développement projet (méthode agile) mise en place chez Eurenco, en m’apportant de la flexibilité dans le design des pièces et des gains importants en termes de temps et de coût, principalement pendant les phases de réitération et d’optimisation du concept. L’équipement issu de cette phase de développement (conception brevetée) permet la réalisation de cordons de matériaux pyrotechniques suivant différentes géométries de dépose ». |
Les auteurs devant l’atelier industriel de Bergerac : Romain Leglise, Chef de programme développement, Damien Chaveroux, Chef de projet études et développement, Clara Debiesse, Ingénieur d’Etudes R&D, Julien Loyer, Technicien Industrialisation, Sébastien Cuvelier, Expert matériaux énergétiques, poudres et objets combustibles.
Aucun commentaire
Vous devez être connecté pour laisser un commentaire. Connectez-vous.