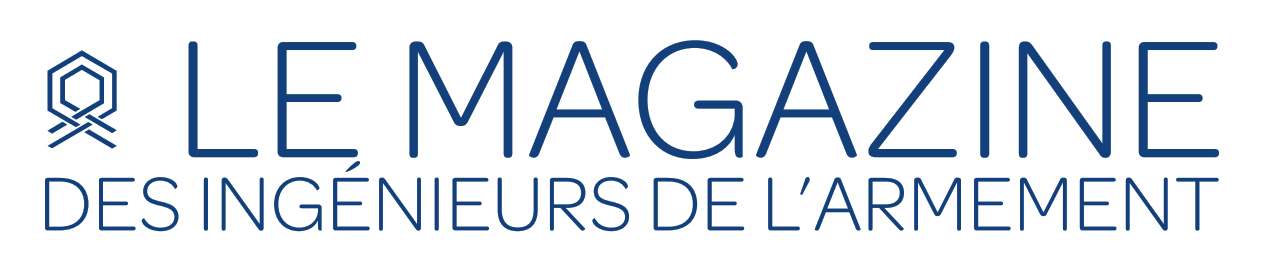
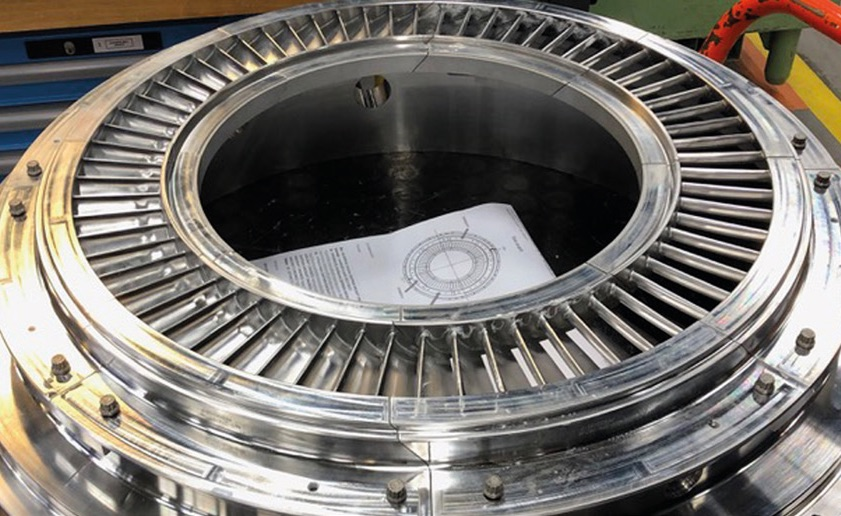
L’AGILITE DANS L’AERONAUTIQUE
Dans l’industrie aéronautique, l’optimisation est telle que le déroulement d’un cycle en V complet d’une machine d’essai peut prendre plusieurs années et le résultat peut donc être obsolète car le produit cible a évolué. Il est donc intéressant d’intégrer les bonnes pratiques du développement agile pour être plus robuste aux changements inhérents de cap.
Si le développement agile est né pour optimiser le développement informatique, ses bonnes pratiques peuvent être reprises et adaptés pour des objets physiques et en particulier industriels.
Pour la génération 2030, Safran développe avec son partenaire historique General Electric le projet Rise. Pour la turbine basse pression du moteur, les régimes de rotation envisagés seront bien supérieurs.
Il s’agit d’une vraie rupture car si les conceptions se sont améliorées et raffinées depuis 50 ans, le concept est resté le même. Ici, on va devoir explorer des comportements jusque-là inconnus.
Les codes de calcul seront nécessairement calibrés dans ce nouveau domaine par des essais. Pour ce faire,
on conçoit, fabrique, monte, instrumente et essaie des démonstrateurs, véhicules de montée en maturité.
Roue de turbine assemblée – chacune de ces aubes de 10cm développe autant de puissance qu’une voiture !
Pourquoi rechercher de l’agilité ?
Les grands paramètres dimensionnants d’une machine d’essai sont fixés dès l’avant-projet : banc retenu, taille, matériaux et donc températures de fonctionnement entre autres.
Or, à ce moment-là, on n’a qu’une idée imparfaite du produit cible. Il faut donc se laisser de la flexibilité pour ajuster en cours de développement. Cela passe par la réduction du délai pour obtenir les résultats (on peut davantage itérer) et la modularité (on prévoit de la marge géométrique pour modifier le design).
Dans une approche classique, le véhicule d’essai est très instrumenté car unique. On souhaite comprendre finement le comportement à l’échelle micro pour en déduire le fonctionnement du produit cible.
Dans une approche agile, on n’étudie que la performance globale sans chercher à comprendre ce qu’il se passe aux petites échelles. Pour ce faire, nos différentes configurations sont des itérations autour d’un point de référence. On étudie un paramètre en laissant les autres fixes.
La tentation de se faire plaisir en R&T
Les ouvriers, techniciens et ingénieurs exercent dans l’aéronautique par passion. Chez Safran, la plupart d’entre eux y passent l’intégralité de leur carrière. Au sein de la direction technique, l’activité de R&T (Recherche et technologie) peut donc concentrer les profils friands de science.
Or, il ne faut jamais perdre de vue le produit final. Les solutions proposées doivent être robustes car les moteurs sont opérés dans des conditions variées (sable, glace) et doivent être peu gourmands en maintenance.
Il peut exister une certaine dérive systémique : les projets sont trop ambitieux ce qui nécessite des boucles de convergence difficiles et longues, ce qui induit du retard et des coûts supplémentaires, réduisant en conséquence le nombre de démonstrateurs entre deux générations de produit.
La situation d’équilibre convergée conduit à faire systématiquement des projets en retard et en dépassement de budget. Un optimum de Pareto (80% du résultat 20% de l’effort) doit être recherché : obtenir rapidement de premiers résultats même imparfaits.
Quelles en sont les causes profondes ?
Introduction de recherche scientifique : on peut vouloir utiliser la machine d’essai comme vecteur pour des essais plus amont (TRL12-3) et donc la sur-instrumenter au-delà du besoin (TRL4-5)
Lassitude des expériences passées et recherche de l’optimisation des ressources : par habitude du retard et parce que les managers ont des objectifs de lissage de charge, on repousse les activités quitte à faire attendre les autres métiers
Annualité des budgets : on souhaite (trop) prédire la consommation annuelle et on repousse donc des livraisons. Au global, cela coûte plus cher car les équipes sont maintenues dans l’attente.
Les projets prennent plus de temps après 3 ans car on est tenté de remettre en cause les choix de son prédécesseur : il est gratifiant de mettre sa touche. Avec une démarche conventionnelle, le démonstrateur fournit toujours de la connaissance. Mais le délai nécessaire (5-6 ans) génère de la frustration dans les équipes et le résultat final est partiellement obsolète.
Une machine modulaire : la recherche de l’efficience et la standardisation
Dans les phases de montée en maturité industrielle (TRL4-5 : validation du sous-système dans un environnement représentatif), on cherche à dégrossir les paramètres dimensionnants et leur sensibilité. Pour cela, nous allons développer une série de turbines (8-10) et nous allons les passer au banc d’essai. Pour limiter les coûts et tester en 18 mois, nous nous appuierons donc sur un véhicule modulaire dans lequel seul le cœur fonctionnel évoluera. Partir gagnant et standardiser le développement de machines d’essai : Partir dans cette démarche nécessite de casser des hypothèses et donc de perdre en représentativité moteur mais en optimisant le ratio valeur/coûts : notre machine sera froide et beaucoup moins instrumentée. Cela nous permet d’utiliser des matériaux performants moins sensibles à la température (du titane) et simplifier
grandement la définition (l’instrumentation a tendance à être très supérieure au besoin). Pour optimiser le délai, chaque métier doit commencer son travail alors que le prédécesseur n’a pas complètement fini : on peut ébaucher des pièces avant de connaitre le diamètre précis au micron. Ça a l’air évident mais c’est très difficile dans un fonctionnement matriciel avec du pointage : on préfère le confort d’avoir tous les éléments figés au début de son étape.
Un tel fonctionnement est bénéfique : on voit le fruit de son travail du dessin à l’assemblage en un an et on apprend de ses erreurs car on ne conçoit pas une machine mais 5-6. On standardise et la configuration supplémentaire a un coût très faible.
Résultat : La machine d’essai précédente a été mise au banc d’essai au bout de 5 ans et son coût avait presque doublé. Dans notre projet STARC, la première configuration a pu être assemblée en moins de 2 ans (l’écart aux 18 mois est imputable aux confinements). En 2 ans, ce sont 5 configurations qui ont pu être lancées et la première a pu vérifier le respect budgétaire. Pour le même coût, on est donc capable de livrer 8 machines, le plus incroyable étant l’introduction d’un essai inédit : on réutilise une configuration pout y introduire des capteurs de vibration. On retrouve ici deux des quatre valeurs du manifeste agile : on doit privilégier une turbine fonctionnelle à l’idée parfaite qui n’aboutit pas et s’adapter au changement. Notre démarche cherche à avoir une première machine le plus tôt possible pour découvrir les problèmes le plus tôt possible (fail fast) afin d’y remédier. Pour atteindre le TRL6 nécessaire du développement d’un moteur (requis par Boeing et Airbus), on devra néanmoins tester une turbine très représentative qui suivra un développement plus classique.
Cette démarche agile n’est pas là pour rejeter le fonctionnement traditionnel, plus intégré dans la marche courante de l’entreprise. Elle nécessite un changement de culture pour apporter plus de savoir au même coût global.
Une machine d’essai modulaire est plus robuste et flexible. On peut introduire des configurations supplémentaires pour tester autre chose (mécanique, instrumentation, fabrication).
Cette expérience s’est inscrite dans le cadre de la période d’ouverture des IA. J’ai pris du plaisir dans ces activités pendant 2 ans et je recommande à tous mes jeunes camarades une expérience dans des activités industrielles et particulièrement dans la production.
Auteur
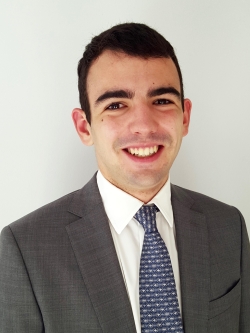
En 2024, il rejoint la Direction Générale du Trésor. Voir les 2 Voir les autres publications de l’auteur(trice)
Aucun commentaire
Vous devez être connecté pour laisser un commentaire. Connectez-vous.